Designing an Effective Supply Chain Organization
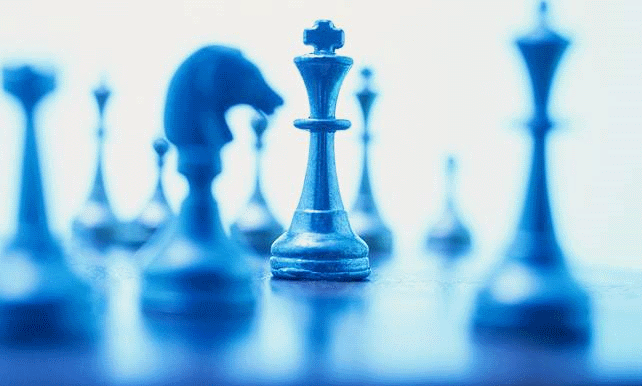
See below for our best practice (baseline) roles & responsibility / RACI matrix download.
Corporate events such as mergers, acquisitions, restructures, and performance improvement programs often bring about a need to examine how supply chain functions should be structured. At one extreme, and still prevalent in many organizations, supply chain duties are scattered throughout the company and have evolved due to the absence of a proactive design effort combined with the necessity of executing day-to-day operations. This is a recipe for duplication of effort, inconsistent practices, people dependent processes, short-term focus, fire-fighting, and higher costs. The higher performing organizations have evolved a long way from here and found ways to integrate supply chain functions into an organizational structure that serves the business while enhancing operational performance. While many principles and design elements can be leveraged across companies and industries, the optimum design is not a “one-size fits all” silver bullet. It must be developed for each unique situation. Here are a few things to keep in mind.
Align the organizational design with your supply chain strategy: A supply chain strategy (definition of items such as customer service approach, production strategy, asset network use, channel strategy) should be defined and aligned with the business strategy (e.g. customer service, product innovation, quality, cost emphasis). Roles should be tailored to fit accordingly. For example, in organizations that prioritize customer service, you might have roles such as dedicated personnel managing VMI replenishment, dedicated customer service representatives for top customers, or more planners to handle more SKUs and configurations. Alternatively in a low cost emphasis organization, you might see fewer or no roles accommodating specialized processes and the emphasis on standardization and scale. The point is to make sure you determine what your emphasis is and design the organization and resulting people cost to accommodate it.
Ensure the supply chain processes are integrated: Break the large processes (e.g. supply chain planning, order fulfillment) into the component sub-processes and make sure hand-offs are well integrated or put them under a single reporting structure. For example, if order taking, sequencing, picking, and logistics are integrated under one management structure, you have a single point of accountability for the execution of the whole process.
Centralized vs. decentralized: This often goes back to aligning with supply chain strategy. Centralization lends itself well to common processes and practices, knowledge sharing, and developing functional expertise. A central supply chain organization can often support multiple business units more effectively at lower cost. In the common case where different business units have different business strategies, central organizations often have specialists by business unit that meet that business unit’s need, but also maintain a common base with others in the same central organization. For example, you may have a demand manager who manages POS data for a consumer products division and another who doesn’t for a B2B division, but the basic demand management process is the same and kept consistent by a common manager or director.
Planning vs. execution: Sometimes it can work well when longer-term planning roles are separate from short-term executional roles. For example you may have a central distribution & logistics function that does the long term modeling and planning for a distribution network for 20 plants, but at each plant you have a short-term transportation scheduler who reports to site management. Depending upon the volume of transportation scheduling required, that person could have other tactical duties as well. In smaller locations, “supply chain people” will often wear multiple hats, the danger can arise when the business at one or many locations grows such that multiple people wear multiple hats and roles become too fragmented.
Sizing: Many supply chain organizations I’ve seen (especially in mid-size companies) have team members that are busy primarily with tactical issues and dealing with the changes in various schedules and/or shipments. Root causes of this are often in upstream process gaps, a lack of customer segmentation, associated service level definition, and rules for handling changes and exceptions. Manufacturing execution can also be an issue. Fire-fighting would be another way to describe all this. Approaches are to address these issues, throw bodies at it, or take the hero approach which isn’t sustainable. Companies aren’t funded for extra people anymore, so we recommend addressing root causes and perhaps a combination of the three while in transition.
Some methods we use include activity analysis based on observations and challenging what really needs to be done, consolidating activities if they are spread out amongst several people, internal/external benchmarking (including span of control analysis), transaction volume analysis/leveling, and IT improvement. It is both art and science. It is important that the staff have time for supply chain analysis otherwise nothing ever improves. It’s also important that there be some level of flexibility to change staffing levels with changes in the business or if first approaches need to be adjusted.
Independence and authority level in the organization: What level in your organization do you want leaders reporting at? Leading companies are generally realizing the importance of supply chain to the organization and have established executive roles (VP) to lead the function. Supply chain leadership and next level down should have enough teeth to be able to maintain independence (i.e. be able to challenge) from executive leaders in sales, marketing, engineering, operations, and finance as supply chain is often in the middle of all of these. A centralized supply chain organization also makes it easier for supply chain professionals to maintain their independence as required.
Career path opportunities: When designing your organization, keep in mind what roles people can move into in the supply chain organization, and where they can move onto from the supply chain organization. Are they relegated to a career certain path, or can they move to other functions and as well?
While this article certainly doesn’t do complete justice to a very large topic, considering these items will help you build a better organization. A structured methodology involving the right people at multiple levels in your organization should be followed to ensure that the best ideas come out, are bought into, and are implemented in your organization. That’s the subject of a future article.
Download our best practice/baseline roles & responsibilities RACI charts for S&OP, supply chain, and interfacing functions
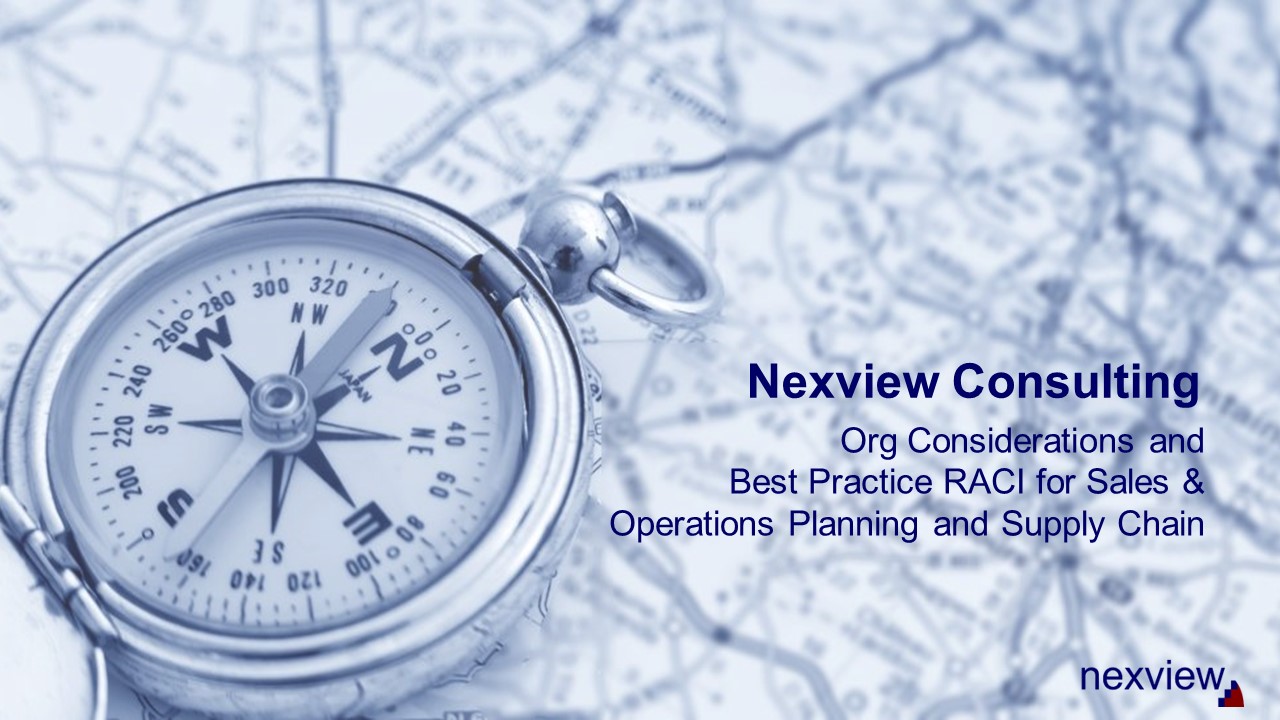
- Additional org considerations
- Supply chain org maturity characteristics
- Roles & responsibilities RACI charts